Easy Anti-Cheat Setup Download and Errors
Unlock the doorway to seamless gaming experiences with the Easy Anti-Cheat Setup and bid farewell to troublesome errors.
- Download and install the tool.
- Perform a full system scan.
- Let the tool automatically correct and maintain your system.
Understanding EasyAntiCheat_Setup.exe: What You Need to Know
EasyAntiCheat_Setup.exe is a crucial file for many games that use Easy Anti-Cheat to prevent cheating. It is responsible for the installation and setup of the anti-cheat software on your system.
To download and install Easy Anti-Cheat, follow these steps:
1. Locate the EasyAntiCheat_Setup.exe file in your game’s installation folder or download it from the game’s launcher or client.
2. Run the EasyAntiCheat_Setup.exe file as an administrator.
3. Follow the on-screen instructions to complete the installation.
4. Once installed, Easy Anti-Cheat will run in the background whenever you launch the game, ensuring a cheat-free gaming experience.
If you encounter any errors during the installation process or while running the game, there are a few troubleshooting steps you can try:
– Repair the Easy Anti-Cheat installation using the repair option in the EasyAntiCheat_Setup.exe file.
– Uninstall Easy Anti-Cheat and reinstall it from scratch.
– Make sure the game and Easy Anti-Cheat have the necessary privileges to run by running them as an administrator.
– Check the game’s installation files for any corrupt or missing files and verify them through the game’s launcher or client.
Remember, Easy Anti-Cheat is essential for maintaining fair gameplay in multiplayer games, so it’s crucial to understand its setup and address any errors promptly.
Latest Update: July 2025
We strongly recommend using this tool to resolve issues with your exe and dll files. This software not only identifies and fixes common exe and dll file errors but also protects your system from potential file corruption, malware attacks, and hardware failures. It optimizes your device for peak performance and prevents future issues:
- Download and Install the Exe and Dll File Repair Tool (Compatible with Windows 11/10, 8, 7, XP, Vista).
- Click Start Scan to identify the issues with exe and dll files.
- Click Repair All to fix all identified issues.
Is EasyAntiCheat_Setup.exe Safe? Exploring Potential Risks
EasyAntiCheat_Setup.exe is a safe program used to prevent cheating in multiplayer games. However, like any software, there are potential risks associated with it. During the installation process, make sure to pay attention to the paths and installation folders to ensure everything is set up correctly. If you encounter any errors during the installation, such as the game not launching or receiving error codes like 30005, there are a few troubleshooting steps you can try. First, check your system’s privileges and ensure you have administrative rights. You can also try force closing the EasyAntiCheat service through the task manager. If all else fails, uninstalling and reinstalling the software may resolve the issue. Remember to always download EasyAntiCheat_Setup.exe from official sources to avoid malware or cheat engine programs.
Common Errors Associated with EasyAntiCheat_Setup.exe
-
Step 1: Check for an active internet connection.
- Ensure that your device is connected to the internet.
- Check if other websites or online services are accessible.
-
Step 2: Update Easy Anti-Cheat Setup.
- Visit the official Easy Anti-Cheat website.
- Download the latest version of EasyAntiCheat_Setup.exe.
- Run the downloaded file and follow the installation instructions.
-
Step 3: Disable antivirus or firewall temporarily.
- Open your antivirus software or firewall settings.
- Temporarily disable any features that may interfere with Easy Anti-Cheat Setup.
- Attempt to run EasyAntiCheat_Setup.exe again.
-
Step 4: Run Easy Anti-Cheat Setup as an administrator.
- Locate the EasyAntiCheat_Setup.exe file on your computer.
- Right-click on the file and select “Run as administrator”.
- Follow the on-screen prompts to complete the installation or repair process.
-
Step 5: Check for conflicting software.
- Review the list of installed software on your computer.
- Identify any programs that may conflict with Easy Anti-Cheat Setup.
- Uninstall or disable those conflicting programs.
- Restart your computer and attempt to run EasyAntiCheat_Setup.exe again.
-
Step 6: Contact Easy Anti-Cheat support.
- Visit the official Easy Anti-Cheat support website.
- Submit a support ticket or seek assistance from their forums.
- Provide detailed information about the error you are experiencing.
How to Repair or Remove EasyAntiCheat_Setup.exe: Step-by-Step Guide
Repairing or removing EasyAntiCheat_Setup.exe can be done easily with the following step-by-step guide:
1. Locate the EasyAntiCheat_Setup.exe file in the installation folder of the game or software. This is typically found in the “bin” or “bin\easyanticheat” folder.
2. If you want to repair EasyAntiCheat, right-click on EasyAntiCheat_Setup.exe and select “Run as administrator”. Follow the on-screen instructions to repair the program.
3. To remove EasyAntiCheat, right-click on EasyAntiCheat_Setup.exe and select “Run as administrator”. Then, choose the “Uninstall” option to remove the software from your system.
4. If you encounter any errors during the repair or removal process, try restarting your computer and running the setup file again.
5. If the above steps don’t work, you can try using the Task Manager to end any EasyAntiCheat processes that might be running in the background.
Remember, these instructions apply to a variety of games and software that use EasyAntiCheat, such as Apex Legends, Fortnite, and Battlefield 2042. By following these steps, you can resolve issues related to EasyAntiCheat_Setup.exe and ensure smooth gameplay without any cheat game interference.
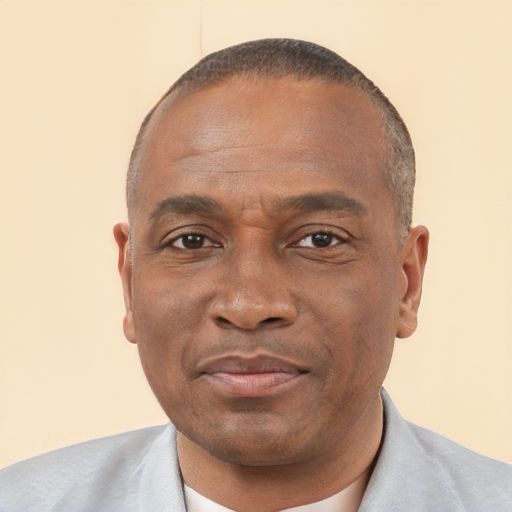