Troubleshooting svchost.exe -k netsvcs -p -s bits and high network activity
In this article, we will explore the troubleshooting process for the svchost.exe -k netsvcs -p -s bits process and its impact on high network activity.
- Download and install the Exe and Dll File Repair Tool.
- The software will scan your system to identify issues with exe and dll files.
- The tool will then fix the identified issues, ensuring your system runs smoothly.
What is svchost.exe -k netsvcs -p -s bits?
The “svchost.exe -k netsvcs -p -s bits” process is a crucial part of the Windows operating system. It is associated with the BITS (Background Intelligent Transfer Service) and is responsible for various tasks related to network activity and updates. However, sometimes this process can cause high CPU usage and network activity, leading to performance issues on your computer.
To troubleshoot this problem, follow these steps:
1. Open the Task Manager by pressing Ctrl + Shift + Esc.
2. Go to the “Processes” tab and find the “svchost.exe” process with the “-k netsvcs -p -s bits” parameters.
3. Right-click on it and select “Go to details.”
4. Note the PID (Process ID) of the process.
5. Open the Resource Monitor by typing “resmon” in the Start menu search bar and selecting the appropriate result.
6. Go to the “CPU” tab and sort the processes by the “PID” column.
7. Find the process with the same PID as the “svchost.exe -k netsvcs -p -s bits” process.
8. Analyze its network activity and CPU usage to determine if it’s causing the problem.
9. If necessary, disable or limit the actions of the BITS service by opening the Services window (type “services.msc” in the Start menu search bar) and modifying the properties of the “Background Intelligent Transfer Service” accordingly.
Is svchost.exe -k netsvcs -p -s bits safe to use?
If you’re experiencing high network activity and are concerned about the safety of the svchost.exe -k netsvcs -p -s bits process, here’s what you need to know.
The svchost.exe -k netsvcs -p -s bits process is a legitimate part of the Windows operating system and is responsible for handling background tasks related to the BITS (Background Intelligent Transfer Service) service.
To troubleshoot high network activity, you can follow these steps:
1. Open Task Manager and go to the “Processes” tab.
2. Right-click on the “svchost.exe” process and select “Go to details”.
3. In the “Details” tab, right-click on the process and choose “Properties”.
4. In the “Properties” window, go to the “Services” tab.
5. Look for the “BITS” service and make sure it is enabled.
6. If the service is disabled, right-click on it and select “Start”.
If you’re still experiencing issues, you can use a process analyzer or resource monitor to identify any specific processes or applications that may be causing the high network activity.
The purpose of svchost.exe -k netsvcs -p -s bits
The svchost.exe -k netsvcs -p -s bits process is a crucial component of the Windows operating system that is responsible for managing various system services. It specifically handles the Background Intelligent Transfer Service (BITS) and its associated functions.
If you are experiencing high network activity or suspect that svchost.exe -k netsvcs -p -s bits is causing performance issues on your computer, there are a few troubleshooting steps you can take:
1. Identify the problem: Use the Task Manager or a process analyzer tool to confirm that svchost.exe -k netsvcs -p -s bits is indeed causing high network usage.
2. Check for Windows updates: Sometimes, high network activity could be due to the Windows Update process. Make sure your computer is up to date by checking for any pending updates.
3. Scan for malware: Malicious software can disguise itself as svchost.exe -k netsvcs -p -s bits, causing high network activity. Use a reliable antivirus or antimalware program to scan your system for any potential threats.
4. Disable unnecessary services: If you only require certain services, you can disable others to reduce network activity. Use the Services console to manage the services running under svchost.exe -k netsvcs -p -s bits.
5. Monitor network usage: Use network monitoring tools to observe the amount of bandwidth being used by svchost.exe -k netsvcs -p -s bits. This can help pinpoint any abnormal activity.
python
import subprocess
def get_svchost_services():
try:
output = subprocess.check_output(['tasklist', '/svc'])
lines = output.decode().split('\n')
for line in lines:
if 'svchost.exe' in line and 'netsvcs' in line:
process_info = line.split()
print(f"Process ID: {process_info[1]}, Services: {process_info[2]}")
except subprocess.CalledProcessError:
print("Failed to retrieve svchost services.")
# Usage
get_svchost_services()
Is svchost.exe -k netsvcs -p -s bits a legitimate file?
If you’re seeing the svchost.exe -k netsvcs -p -s bits process running on your computer and are experiencing high network activity, you may be wondering if it’s a legitimate file. The answer is yes, svchost.exe -k netsvcs -p -s bits is a legitimate file that is used by the Windows operating system.
This particular svchost.exe process is responsible for running various services related to network communication, including the Background Intelligent Transfer Service (BITS). BITS is a service that allows for the transfer of files between machines on a network.
If you are experiencing high network activity and suspect that the svchost.exe -k netsvcs -p -s bits process may be the cause, there are a few troubleshooting steps you can take. First, check the Windows Update service to see if it is currently downloading updates. If so, this could be the cause of the high network activity.
You can also check the Event Viewer for any error messages related to the BITS service. If you find any, try restarting the BITS service to see if that resolves the issue. Additionally, check for any malware or viruses on your computer, as they can sometimes cause high network activity.
Should I delete svchost.exe -k netsvcs -p -s bits?
If you are experiencing high network activity and suspect that svchost.exe -k netsvcs -p -s bits is causing the issue, you may consider deleting it. However, before taking any action, it is important to understand the potential consequences.
Deleting svchost.exe -k netsvcs -p -s bits can lead to system instability and may cause other services to malfunction. It is recommended to first analyze the problem and identify the root cause.
To troubleshoot the issue, try the following steps:
1. Open the Task Manager by pressing Ctrl + Shift + Esc.
2. Locate the svchost.exe process with the description “netsvcs” and “bits”.
3. Right-click on the process and select “Open File Location”.
4. Verify that the file is located in the System32 folder. If it is not, it may be malware.
5. If the file is in the correct location, it is likely a legitimate system process and deleting it is not recommended.
6. If you suspect malware, run a thorough scan using a trusted antivirus or anti-malware software.
7. If the high network activity persists, consider seeking assistance from a professional or a dedicated troubleshooting forum.
Keep in mind that deleting system files without proper knowledge can have serious consequences. It is always better to err on the side of caution and seek expert advice if you are unsure about the best course of action.
The origin of svchost.exe -k netsvcs -p -s bits
svchost.exe -k netsvcs -p -s bits is a process in the Microsoft Windows Operating System that is responsible for managing network services. It can sometimes cause high network activity, which can be a concern for users.
One possible reason for this high network activity is the IP Helper Service, which is a Windows service that provides support for Internet Protocol version 6 (IPv6) connectivity. If this service is enabled, it can consume a significant amount of bandwidth.
To troubleshoot this issue, you can try disabling the IP Helper Service by following these steps:
1. Press the Windows key + R to open the Run dialog box.
2. Type “services.msc” and press Enter.
3. Scroll down and find the “IP Helper” service.
4. Right-click on it and select “Properties.”
5. In the Properties window, change the “Startup type” to “Disabled.”
6. Click on “Apply” and then “OK” to save the changes.
Disabling the IP Helper Service should help reduce the high network activity caused by svchost.exe -k netsvcs -p -s bits.
How to use svchost.exe -k netsvcs -p -s bits
To troubleshoot high network activity caused by svchost.exe -k netsvcs -p -s bits, follow these steps:
1. Open the Task Manager by pressing Ctrl + Shift + Esc.
2. In the Processes or Details tab, locate and right-click on the svchost.exe -k netsvcs -p -s bits process.
3. Select “Go to Services” from the context menu.
4. This will take you to the Services tab with the corresponding service highlighted.
5. Identify the service causing high network activity. Common culprits include Windows Update, BITS (Background Intelligent Transfer Service), or Windows Update Medic Service.
6. Once identified, you can take specific actions to troubleshoot the issue:
– For Windows Update, check for pending updates and let them install.
– For BITS, restart the service by opening an elevated Command Prompt and typing “net stop bits” followed by “net start bits“.
– For Windows Update Medic Service, disable it temporarily and check if the network activity decreases.
7. Monitor the network activity using the Task Manager or a network monitoring tool to ensure the issue is resolved.
Is svchost.exe -k netsvcs -p -s bits a malware?
If you are experiencing high network activity and have come across the svchost.exe -k netsvcs -p -s bits process, you may be wondering if it is malware. In most cases, this process is not malware, but a legitimate part of the Windows operating system.
However, it is important to note that malware can sometimes disguise itself as this process. To determine if it is malware, you can follow these steps:
1. Open the Task Manager by pressing Ctrl + Shift + Esc.
2. Locate the svchost.exe -k netsvcs -p -s bits process in the Processes tab.
3. Right-click on it and select “Open File Location.”
4. If the file is located in the C:\Windows\System32 folder, it is likely not malware.
5. If the file is located somewhere else, or if you notice any suspicious behavior, it may be malware.
If you suspect malware, it is recommended to run a full system scan with a trusted antivirus or antimalware program. Additionally, you can seek assistance from online forums or contact a professional for further troubleshooting.
Unable to delete svchost.exe -k netsvcs -p -s bits
If you’re unable to delete the svchost. exe -k netsvcs -p -s bits process and experiencing high network activity, there are a few troubleshooting steps you can try. First, make sure to run a scan with your security solution to check for any malware or viruses. You can also try restarting your computer in safe mode and deleting the process from there. Additionally, you can use the Task Manager to end the process, disable any unnecessary startup programs, and clear your cookies and cache. If the issue persists, you may want to seek assistance from online forums like tenforums.
com or contact the site owner for further support.
Understanding svchost.exe -k netsvcs -p -s bits running in the background
If you notice high network activity and the process svchost.exe -k netsvcs -p -s bits running in the background on your Windows PC, it is important to troubleshoot the issue. This process is responsible for Windows update downloads and can sometimes cause high network usage.
To troubleshoot this issue, follow these steps:
1. Open the Task Manager by pressing Ctrl+Shift+Esc.
2. Locate the svchost.exe -k netsvcs -p -s bits process in the Processes tab.
3. Right-click on the process and select “Go to Services.”
4. In the Services tab, find the “Background Intelligent Transfer Service (BITS)” and “Windows Update” services.
5. Stop both services and then restart them.
6. Check if the high network activity has reduced.
If the issue persists, you can also try resetting the Windows Update components. To do this, open the Command Prompt as an administrator and run the following commands:
net stop wuauserv
net stop cryptSvc
net stop bits
net stop msiserver
ren C:\Windows\SoftwareDistribution SoftwareDistribution.old
ren C:\Windows\System32\catroot2 catroot2.old
net start wuauserv
net start cryptSvc
net start bits
net start msiserver
These steps should help resolve any issues with svchost.exe -k netsvcs -p -s bits and high network activity.
High CPU usage caused by svchost.exe -k netsvcs -p -s bits
If you’re experiencing high CPU usage caused by “svchost.exe -k netsvcs -p -s bits” and also noticing high network activity, there are a few troubleshooting steps you can take.
First, open the Task Manager by pressing Ctrl + Shift + Esc and locate the “svchost.exe” process with the “netsvcs” parameter. Right-click on it and select Go to Services to identify the specific service causing the issue.
Next, open the Services window by pressing Win + R and typing “services.msc”. Locate the service that corresponds to the problematic svchost process and right-click on it, selecting Stop.
To prevent the service from starting automatically, right-click on it again and choose Properties. Under the General tab, change the Startup type to Disabled.
If the issue persists, it may be helpful to consult online forums like tenforums.com or contact Microsoft support for further assistance.
svchost.exe -k netsvcs -p -s bits as a system file
If you’re experiencing high network activity and suspect that the svchost.exe -k netsvcs -p -s bits process is causing it, here’s what you can do to troubleshoot the issue:
1. Open the Task Manager by pressing Ctrl + Shift + Esc.
2. In the Processes tab, locate the svchost.exe -k netsvcs -p -s bits process.
3. Right-click on it and select End Process.
4. If the problem persists, open the Command Prompt as an administrator.
5. Type net stop bits and press Enter to stop the Background Intelligent Transfer Service (BITS).
6. Next, type net start bits and press Enter to start the BITS service again.
7. Check if the high network activity has subsided.
If the issue continues, it may be worth seeking assistance from online forums like tenforums.com or consulting with your organization’s IT support.
Latest Update: July 2025
We strongly recommend using this tool to resolve issues with your exe and dll files. This software not only identifies and fixes common exe and dll file errors but also protects your system from potential file corruption, malware attacks, and hardware failures. It optimizes your device for peak performance and prevents future issues:
- Download and Install the Exe and Dll File Repair Tool (Compatible with Windows 11/10, 8, 7, XP, Vista).
- Click Start Scan to identify the issues with exe and dll files.
- Click Repair All to fix all identified issues.
Associated software with svchost.exe -k netsvcs -p -s bits
- Windows Update Service: This service is responsible for downloading and installing updates for the Windows operating system.
- Background Intelligent Transfer Service (BITS): BITS is a Windows service that facilitates asynchronous and prioritized transfer of files between a client and a server.
- Update Orchestrator Service (UsoSvc): UsoSvc is responsible for managing the installation and coordination of Windows updates.
- Cryptographic Services (CryptSvc): CryptSvc provides essential cryptographic functions to Windows components, such as secure communication and data encryption.
- Server (LanmanServer): The LanmanServer service enables file and printer sharing on a local network.
- Security Accounts Manager (SAM): SAM manages user accounts and security policies on a Windows system.
- Windows Event Log (EventLog): EventLog records system events and notifications on a Windows computer.
- Windows Management Instrumentation (Winmgmt): Winmgmt provides a set of tools and interfaces for managing and querying system information.
- Windows Firewall (MpsSvc): MpsSvc is responsible for managing the Windows Firewall and its associated security settings.
- Windows Modules Installer (TrustedInstaller): TrustedInstaller is used for installing, modifying, and removing Windows updates and optional components.
Creator of svchost.exe -k netsvcs -p -s bits
If you are experiencing high network activity and have identified the svchost.exe -k netsvcs -p -s bits process as the culprit, there are a few troubleshooting steps you can take.
Firstly, open the Task Manager and locate the svchost.exe -k netsvcs -p -s bits process. Right-click on it and select “End task” to stop it temporarily.
Next, clear your cookies and cache by going to your browser settings. This can help resolve any issues related to website security services like Cloudflare.
If the high network activity persists, you can try disabling the IP version 6 (IPv6) on your Windows 7 or Windows 10 PC. This can sometimes resolve network-related issues.
Additionally, check the Event Viewer for any error reports related to the svchost.exe process. This may provide more insight into the issue.
If none of these troubleshooting steps work, it might be worth contacting your organization’s IT support or a professional technician for further assistance.
Is it safe to end task svchost.exe -k netsvcs -p -s bits?
Ending the task svchost.exe -k netsvcs -p -s bits is not recommended unless you are experiencing specific issues related to high network activity or troubleshooting. The svchost.exe process is a vital part of the Windows operating system and terminating it can cause system instability.
If you are facing high network activity or suspect that the svchost.exe process is causing performance issues, it is advisable to investigate the underlying cause rather than ending the task.
To troubleshoot the issue, you can try the following steps:
1. Check for malware or virus infections using a reliable security solution.
2. Use the Windows Task Manager to identify which specific service is causing the high network activity.
3. Update your Windows operating system to the latest version to fix any known issues.
4. Consult online forums or support communities for further assistance with specific troubleshooting questions.
Description of svchost.exe -k netsvcs -p -s bits process
The svchost.exe -k netsvcs -p -s bits process is a part of the Microsoft Windows Operating System and is responsible for handling various tasks related to network services. However, sometimes this process can cause high network activity, leading to performance issues on your PC.
If you are experiencing this problem, there are a few troubleshooting steps you can try. First, you can try restarting your computer to see if that resolves the issue. If not, you can use the Task Manager to end the svchost.exe -k netsvcs -p -s bits process.
If the problem persists, you may need to investigate further by checking for any recent Windows updates or malware infections. You can also try disabling any unnecessary network services that may be causing the high network activity.
svchost.exe -k netsvcs -p -s bits not responding
1. Check for malware or malicious activity on your PC using a reliable antivirus program.
2. Restart your computer and see if the issue persists.
3. Disable the BITS (Background Intelligent Transfer Service) service temporarily and see if the problem goes away. Use the command net stop bits in the Command Prompt to stop the service.
4. Update your Windows operating system to the latest version. Sometimes, update errors can cause svchost.exe issues.
5. If you’re using Windows 7, try running the Windows Update Troubleshooter tool to identify and fix any update-related problems.
6. Consider checking if there’s a memory leak issue with the svchost process. You can use tools like Process Explorer to monitor memory usage.
7. If you’re using Windows 10, try performing a clean boot to identify any third-party software conflicts that may be causing the problem.
Removal tool for svchost.exe -k netsvcs -p -s bits
If you are experiencing high network activity and suspect that the svchost.exe -k netsvcs -p -s bits process is causing it, you may need to use a removal tool. This tool will help you identify and eliminate any issues related to this process.
To begin, download a reputable removal tool from a trusted source. Once downloaded, run the tool and follow the on-screen instructions to scan your system for any traces of svchost.exe -k netsvcs -p -s bits.
If the tool detects any suspicious activity or files, it will provide you with options to remove or quarantine them. Select the appropriate action and let the tool do its work.
After the removal process is complete, restart your computer to ensure all changes take effect. Monitor your network activity to see if the issue has been resolved. If you still experience high network activity, consider seeking further assistance from a professional or your organization’s IT department.
svchost.exe -k netsvcs -p -s bits startup behavior
First, check for any malware or virus infections on your system. Malware can sometimes disguise itself as svchost.exe, causing high network usage. Run a thorough scan using a reputable antivirus software to eliminate any potential threats.
Next, disable the BITS (Background Intelligent Transfer Service) if it is not required for your system. BITS is responsible for transferring files in the background, and disabling it can help reduce network activity. To do this, open the Services console (press Windows + R, type “services.msc” and hit Enter), locate “Background Intelligent Transfer Service,” right-click on it, and select “Properties.” Change the Startup type to “Disabled” and click “Apply” and “OK.”
If the issue persists, check for Windows updates that might fix any bugs or errors related to svchost.exe -k netsvcs -p -s bits. Open the Windows Update settings and check for any available updates. Install them and restart your system if necessary.
Remember to monitor your network activity regularly using the Task Manager or a network monitoring tool. Identify any suspicious processes or excessive network usage and investigate further if needed.
Troubleshooting svchost.exe -k netsvcs -p -s bits issues
- Step 1: Open Task Manager by pressing Ctrl+Shift+Esc.
- Step 2: In the Task Manager window, click on the Processes tab.
- Step 3: Locate the svchost.exe -k netsvcs -p -s bits process in the list.
- Step 4: Right-click on the svchost.exe -k netsvcs -p -s bits process and select End Task.
- Step 5: Confirm the action by clicking End Process in the confirmation dialog box.
- Step 6: Open the Run dialog box by pressing Windows Key + R.
- Step 7: Type services.msc in the Run dialog box and press Enter.
- Step 8: In the Services window, locate the Background Intelligent Transfer Service (BITS).
- Step 9: Right-click on the Background Intelligent Transfer Service (BITS) and select Restart.
- Step 10: Close all open windows and restart your computer.
Performance impact of svchost.exe -k netsvcs -p -s bits
The svchost.exe -k netsvcs -p -s bits process can have a significant impact on your computer’s performance and network activity.
One common issue is high network usage, which can slow down your internet connection and overall system performance. This is often caused by the BITS (Background Intelligent Transfer Service) component, which is responsible for transferring files in the background.
To troubleshoot this issue, you can try the following steps:
1. Open Task Manager by pressing Ctrl + Shift + Esc and go to the “Processes” tab.
2. Look for the svchost.exe process with the description “netsvcs” and high CPU or memory usage.
3. Right-click on the process and select “End Process Tree” to stop it temporarily. Note that this may affect certain services or applications.
4. If the high network activity persists, you can disable the BITS service by following these steps:
a. Press Win + R to open the Run dialog box.
b. Type “services.msc” and press Enter.
c. Locate the “Background Intelligent Transfer Service” in the list and double-click on it.
d. Change the startup type to “Disabled” and click on “Apply” and “OK”.
5. Restart your computer and monitor the network activity to see if the issue is resolved.
Updating svchost.exe -k netsvcs -p -s bits
If you’re experiencing high network activity and have identified the svchost.exe -k netsvcs -p -s bits process as the culprit, updating it might help resolve the issue.
To update svchost.exe -k netsvcs -p -s bits, follow these steps:
1. Press Windows Key + R to open the Run dialog box.
2. Type services.msc and press Enter to open the Services window.
3. Scroll down and locate the Background Intelligent Transfer Service (BITS) entry.
4. Right-click on it and select Properties.
5. In the Properties window, click on the General tab.
6. Click the Stop button to stop the service.
7. Go to the official Microsoft website and search for the latest BITS update.
8. Download and install the update according to the provided instructions.
9. Once the update is installed, go back to the Services window and start the Background Intelligent Transfer Service (BITS) again.
10. Check if the high network activity issue has been resolved.
Downloading svchost.exe -k netsvcs -p -s bits
If you are experiencing high network activity and notice the process “svchost.exe -k netsvcs -p -s bits” consuming a lot of resources, it may indicate a problem with BITS (Background Intelligent Transfer Service). To troubleshoot this issue, follow these steps:
1. Check for malware: Run a full scan with a reputable antivirus software to ensure your system is not infected.
2. Restart BITS service: Open the Services application (press Windows key + R, then type “services.msc”) and locate the “Background Intelligent Transfer Service”. Right-click on it and select “Restart”.
3. Clear BITS queue: Open Command Prompt as administrator and run the command “bitsadmin.exe /reset /allusers”.
4. Update Windows: Make sure your operating system is up to date by checking for Windows updates.
If the issue persists, it may require further investigation or assistance from a technical professional.
Compatibility with different Windows versions
When troubleshooting the svchost.exe -k netsvcs -p -s bits and high network activity issue, it’s important to consider the compatibility with different Windows versions.
First, ensure that your Windows version is supported by the troubleshooting steps provided. Some steps may be specific to certain Windows versions, so double-check the instructions before proceeding.
If you’re unsure of your Windows version, you can determine it by right-clicking on the “My Computer” or “This PC” icon and selecting “Properties.” The Windows version will be listed under the “System” section.
Keep in mind that troubleshooting steps may vary slightly depending on the version of Windows you’re using. It’s essential to follow the instructions relevant to your specific Windows version to avoid any compatibility issues.
By ensuring compatibility with your Windows version, you can effectively troubleshoot the svchost.exe -k netsvcs -p -s bits and high network activity problem on your PC.
Alternatives to svchost.exe -k netsvcs -p -s bits
If you’re experiencing high network activity and encountering the svchost.exe -k netsvcs -p -s bits process, there are a few alternatives you can try to troubleshoot the issue.
1. Check for malware or viruses: Run a thorough scan using a reliable antivirus program to ensure that your system is free from any malicious software.
2. Restart the BITS service: Open the Command Prompt as an administrator and type “net stop bits” followed by “net start bits” to restart the Background Intelligent Transfer Service.
3. Disable Windows Update temporarily: Open the Control Panel, go to Windows Update settings, and select “Never check for updates“. This will prevent Windows from automatically downloading updates and potentially causing the high network activity.
4. Check for memory leaks: Use the Task Manager to monitor the memory usage of the svchost.exe -k netsvcs -p -s bits process. If it consistently consumes a large amount of memory, it may be a memory leak issue. In this case, consider updating your device drivers or contacting the manufacturer for further assistance.
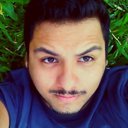